Новые разработки
И хотя полимеризация в ванне - самая первая из технологий 3D-печати, не много инноваций коснулось ее за последние 10 лет. Одной из наиболее ожидаемой инновацией в этой области было изобретение непрерывной печати.
Прямая обработка светом – Carbon
По методу Постоянной прямой обработки светом (Continuous Direct Light Processing - CDLP) детали производятся так же, как и по методу DLP, однако CDLP обеспечивает постоянное движение рабочей платформы по оси Z (вверх). Компания Carbon использует эту технологию в коммерческих целях. Технология Digital Light Synthesis™ (Синтез цифрового света), разработанная в компании, похожа на CDLP. Она работает на основе процесса Постоянного производства поверхности жидкости (Continuous Liquid Interface Production -CLIP).
Принтеры М-серии от Carbon используют специализированный фотополимер в сочетании с воздухопроницаемым окном для создания «мертвых зон» незасвеченного связующего вещества на дне ванны. В результате низ печатного образца никогда не прилипает ко дну ванны, то есть исчезает необходимость этапа отделения, необходимого для многих принтеров, печатающих снизу-вверх. Это позволяет существенно увеличить время печати, так как не нужно останавливать принтер и отделять деталь от рабочей платформы после печати каждого слоя. Также, это значит, что детали, по сути, являются изотропными, так как слои не печатаются индивидуально. Принтеры компании Carbon печатают снизу-вверх.
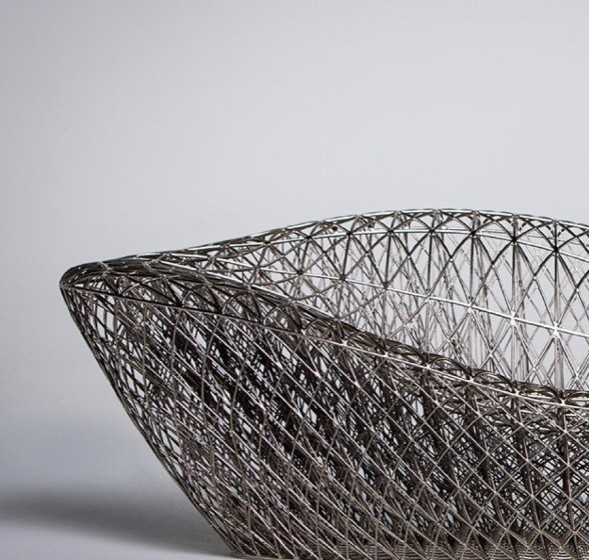